For decades, pneumatic and hydraulic actuators have been go-to technologies in the industrial automation space, but they have as many drawbacks as advantages, particularly pneumatic actuators. Meanwhile, electric cylinders have made great strides, to the point where OEMs and system integrators are increasingly choosing them whenever possible. Compared to pneumatic and hydraulic technologies, electric cylinders offer significantly higher efficiency and positioning performance, as well as reduced maintenance and downtime in a smaller package. The result is the lowest total cost of ownership (TCO) of the three technologies.
With ongoing technical advances, electric cylinders can generate forces that are competitive with pneumatic actuators and with a percentage of hydraulic actuators. For industrial applications, pneumatic and hydraulic cylinders should no longer be considered a given. Let’s look at seven reasons why you should consider electric cylinders for your next project. Actuator Motors
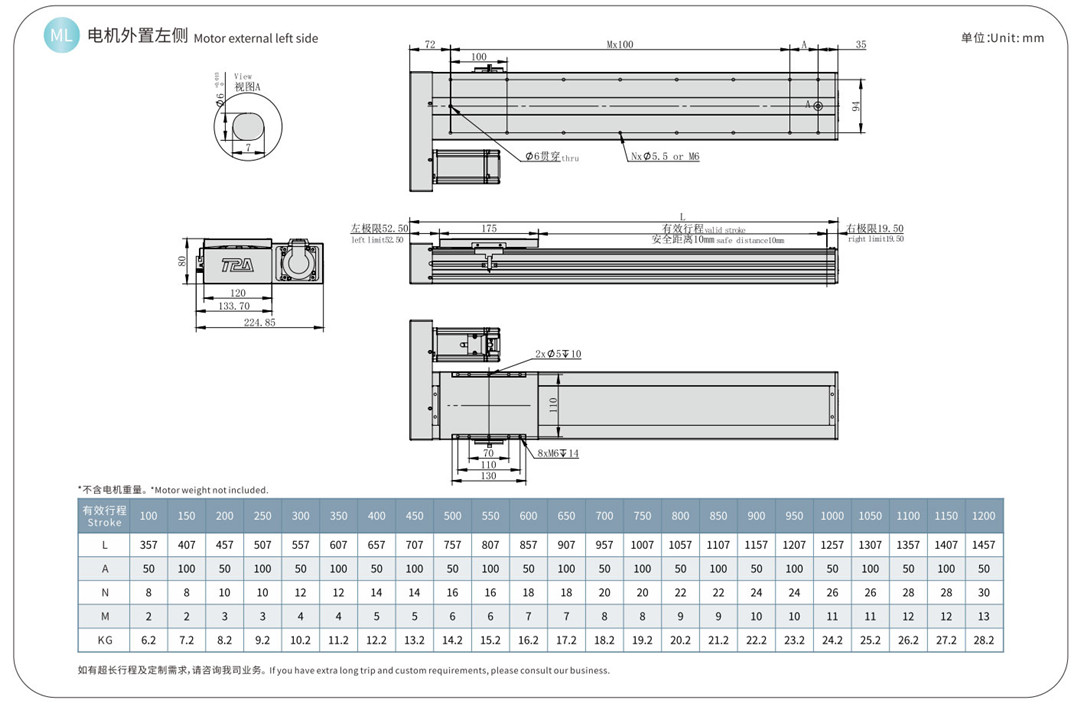
The common terminology is to call pneumatic and hydraulic actuators cylinders, but that’s incorrect. These are actually system-level solutions:
Pneumatic Actuators: Pneumatic actuators generate motion through compressed air. A typical pneumatic actuator consists of an air cylinder, a compressor or compressed-air supply, hoses, and ancillary devices like seals, valves, regulators, filters, etc. Single-action cylinders use compressed air for a single direction and a spring for the return. Double action pneumatic cylinders use compressed air for both extension and retraction.
Hydraulic Actuators: Hydraulic actuators use a similar model to pneumatic actuators, except that instead of transferring force via compressed air, they use a non-compressible hydraulic fluid. The actuator consists of a hydraulic cylinder, a pump, a fluid reservoir, ancillary filters, etc.
Electric Cylinders: Electric cylinders use an electric motor to drive a rod-style actuator (see Figure 1). Outside of the motor drive and feedback device (typically an encoder), they just need cabling to operate. Electric cylinders provide a number of advantages over pneumatic and hydraulic actuators.
Figure 1: An electric cylinder, like the Beckhoff AA3000, consists of an electric motor driving a threaded rod-style actuator.
One of the biggest drawbacks to pneumatic and hydraulic actuators is that the compressors or pumps need to run constantly to keep the lines charged, even when the cylinders are idle. Pneumatic actuator efficiencies range from 10% to 25%, although that number drops over time as seals degrade and leaks develop in the supply hoses. Hydraulic actuators are a bit better at roughly 40% efficiency.
In contrast, electric cylinders draw power only when the motor is turning to move the cylinder. As a result, they can achieve efficiencies as high as 80%, for a substantially lower energy consumption than the other two technologies. This is an important point, particularly since the lifetimes of industrial assets are expected to be measured in decades. A pneumatic actuator can have a lower total cost of acquisition (TCA) than an electric cylinder, but an electric cylinder will have a significantly TCO over the life of the product.
The thinking used to be that hydraulic cylinders offer the most force, followed by pneumatic cylinders, then electric cylinders. That situation has changed. Advanced electric cylinders like the AA3000 can produce peak forces as high as 25 kN (see sidebar). That’s a match for any pneumatic actuator. Electric cylinders are not being positioned as a blanket replacement for all hydraulic actuators, but they are viable options in a significant percentage of cases, especially given the other capabilities they bring such as…
Electric cylinders deliver full servo-based motion control functionality. They offer high accuracy and repeatability; resolution depends on feedback and the mechanical fidelity of the system. Electric cylinders can direct the load to any position across the length of stroke and support complex acceleration profiles. Backlash depends on the mechanical elements of the system, particularly the gearbox, but is consistently better than pneumatic actuators.
Pneumatic and hydraulic actuators can only position accurately at the extremes of stroke. Mid-stroke positioning requires servo valves that add complexity and cost without meeting the accuracy, repeatability, and resolution of electric cylinders. Any leakage of seals and hoses as equipment ages will compromise performance and require constant adjustment. Changing velocity is extremely challenging.
Because pneumatic actuators use compressed air, there’s a certain amount of compliance, or sponginess, when they’re back driven. Hydraulic fluid is non-compressible, so hydraulic actuators don’t suffer from this issue. Electric cylinders can have backlash, but only on reversal and it is generally well-controlled – for the AA3000, it can be as low as 15 µm.
Meet the AA3000 Electric Cylinder from Beckhoff
Pneumatic and hydraulic actuators are multi-part systems that are labor-intensive to maintain. Hoses leak, seals degrade, and the pumps and compressors themselves require maintenance. Although the induction motors that power compressors and pumps can be monitored through vibration analysis, advance warning systems for issues like leaks in hoses is more difficult. In the case of pneumatic cylinders, leaks significantly increase power consumption while compromising performance, but troubleshooting can be very time-consuming. In the case of hydraulic actuators, the leaks will be very obvious – and very messy. In both cases, maintenance teams can spend a large amount of time inspecting the system in an effort to maintain performance, which can be very expensive. There is also the ever-present task of cleaning up leaking hydraulic fluid.
Electric cylinders have far fewer points of failure – no hoses, valves, flowmeters, compressors, pumps, etc. Although there is a seal around the rod of the actuator, it is not directly related to system performance and doesn’t impact accuracy, repeatability, or power consumption. Electric cylinders track position using encoders, which are much more robust and reliable than the mechanical devices like reed switches that are used by pneumatic and hydraulic actuators. Even better, electric cylinders have well-established predictive maintenance capabilities that give advance warnings of developing issues, making it possible to schedule maintenance at convenient times.
Pneumatic and hydraulic positioning is based on fluid flow, so initial set up and commissioning can be time-consuming and complex. Electric cylinders are software controlled. Their reputation for complexity is outdated – many industrial systems feature auto configuration and streamlined user interfaces for fast commissioning. (see Figure 2). For OEMs and system integrators assembling a machine, time is money. Commissioning speed is an important advantage for end users as well.
Figure 2: Streamlined configuration software for the AA3000 makes motion profile selection as easy as point and click.
Electric cylinder technology really shines when it’s time to change motion parameters. For pneumatic and hydraulic actuators, the process of calculating pressures and adjusting (and adjusting, and adjusting…) valves to achieve the desired position and velocity begins all over again. In the case of electric cylinders, changeovers just require a software update, or choosing a different recipe from the HMI menu.
Electric cylinders also simplify machine safety implementation. Pneumatic and hydraulic cylinders require external sensors and relays, which can be complex, expensive, and time-consuming to implement, while further increasing the footprint of the system. Electric cylinders are now available with integrated safety capabilities that can be implemented with simple configuration screens.
Electric cylinders have a smaller footprint than pneumatic or hydraulic actuators that have the same force rating. They don’t need compressors or pumps, or the sometimes-extensive supply hoses required by pneumatic and hydraulic solutions. Some electric cylinders may have external drives either on the machine or in a cabinet, but versions with integrated motors, like the Beckhoff AA3000, are increasingly common.
The combination of higher efficiencies, reduced maintenance, and better ease-of-use add up to lower TCO for electric cylinders. In high force applications, electric cylinders deliver faster ROI than pneumatic cylinders.
Modern electric cylinders provide a host of advantages over pneumatic actuators and many hydraulic actuators. With increased efficiency and ease of use, along with reduced maintenance requirements, electric cylinders offer users significantly lower TCO. Meanwhile, electric cylinders also deliver vastly better performance than the alternatives, with complete motion control capabilities and higher accuracy, repeatability, and resolution. Just as important, continued technology advances have resulted in electric cylinders capable of peak forces as high as 25 kN. To this, add a smaller footprint – always a consideration in the crowded factory environment – to the host of reasons to consider electric cylinders for your next application.
To learn more about the Beckhoff AA3000 electric cylinder and what it can do for you, contact [email protected]
Browse the most current issue of Design World and back issues in an easy to use high quality format. Clip, share and download with the leading design engineering magazine today.
Top global problem solving EE forum covering Microcontrollers, DSP, Networking, Analog and Digital Design, RF, Power Electronics, PCB Routing and much more
The Engineering Exchange is a global educational networking community for engineers. Connect, share, and learn today »

High Load Linear Actuator Copyright © 2023 WTWH Media LLC. All Rights Reserved. The material on this site may not be reproduced, distributed, transmitted, cached or otherwise used, except with the prior written permission of WTWH Media Privacy Policy | Advertising | About Us